在生物制藥生產(chǎn)中,一個(gè)直徑僅0.1毫米的微孔或一道0.01微米的表面劃痕,都可能成為微生物滋生的溫床,直接導(dǎo)致價(jià)值數(shù)百萬(wàn)美元的藥品批次報(bào)廢。
生物制藥專用閥門作為流體控制系統(tǒng)的核心組件,通過(guò)材料革新、結(jié)構(gòu)優(yōu)化與智能控制三大技術(shù)突破,構(gòu)建起覆蓋全流程的無(wú)菌屏障,成為保障藥品質(zhì)量與生產(chǎn)安全的“隱形守護(hù)者”。
1.超潔凈材料:從分子層面阻斷污染
生物制藥閥門主體采用316L不銹鋼或聚四氟乙烯(PTFE)等惰性材料,其表面經(jīng)過(guò)機(jī)械拋光(Ra≤0.25μm)與電解拋光(Ra≤0.1μm)雙重處理,較工業(yè)閥門降低80%的表面粗糙度。某德國(guó)品牌隔膜閥通過(guò)在316L閥體內(nèi)襯0.5mm厚PTFE涂層,將蛋白吸附率從0.5mg/cm2降至0.02mg/cm2,成功應(yīng)用于單抗藥物生產(chǎn)。密封件則選用符合USP Class VI標(biāo)準(zhǔn)的EPDM或FFKM橡膠,經(jīng)伽馬射線滅菌后拉伸強(qiáng)度保持率>95%,確保長(zhǎng)期密封可靠性。
2.360°流道:消除交叉污染風(fēng)險(xiǎn)
傳統(tǒng)閥門90°彎角處的流體滯留區(qū)是微生物滋生的重災(zāi)區(qū)。生物制藥閥門創(chuàng)新采用全通徑或斜角流道設(shè)計(jì),配合CFD模擬優(yōu)化技術(shù),將殘留體積從1.2ml降至0.05ml。某無(wú)菌級(jí)球閥通過(guò)流道優(yōu)化,使細(xì)胞培養(yǎng)基殘留率降低98%,顯著降低批次間交叉污染風(fēng)險(xiǎn)。三通抗生素截止閥更以螺旋流道與雙重關(guān)閉設(shè)計(jì),實(shí)現(xiàn)零死角、零泄漏,在抗生素發(fā)酵工藝中染菌率降低至0.003%。
3.智能控制:精準(zhǔn)駕馭生命流體
在細(xì)胞培養(yǎng)基補(bǔ)料環(huán)節(jié),微型針閥通過(guò)壓電陶瓷驅(qū)動(dòng)技術(shù),實(shí)現(xiàn)0.1-10ml/min的精準(zhǔn)投料,流量重復(fù)性誤差<±0.5%,避免營(yíng)養(yǎng)失衡導(dǎo)致的細(xì)胞凋亡。某多通道分液閥集成雙密封圈與自排水結(jié)構(gòu),確保121℃高溫滅菌蒸汽100%穿透流道,滅菌驗(yàn)證符合FDA 21 CFR Part 11要求。更值得關(guān)注的是,模塊化設(shè)計(jì)使閥門可與一次性生物反應(yīng)器、層析系統(tǒng)無(wú)縫對(duì)接,某品牌無(wú)菌取樣閥采用Luer鎖接口與預(yù)滅菌包裝,單次使用成本降低40%,安裝時(shí)間從2小時(shí)縮短至15分鐘。
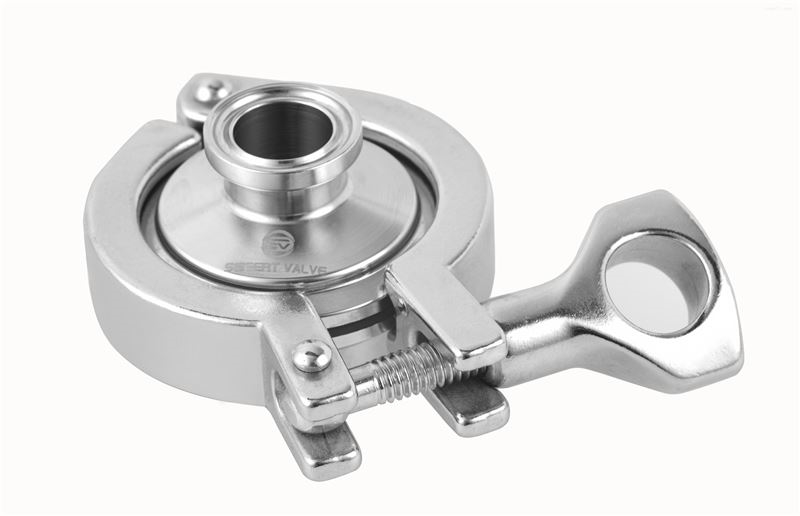
從上游細(xì)胞培養(yǎng)到下游制劑灌裝,生物制藥專用閥門正以“分子級(jí)”精度重新定義藥品生產(chǎn)的潔凈標(biāo)準(zhǔn)。隨著CAR-T療法、mRNA疫苗等新興領(lǐng)域的崛起,這些閥門正向智能化、微型化方向加速進(jìn)化,成為推動(dòng)生物醫(yī)藥產(chǎn)業(yè)高質(zhì)量發(fā)展的“隱形引擎”。